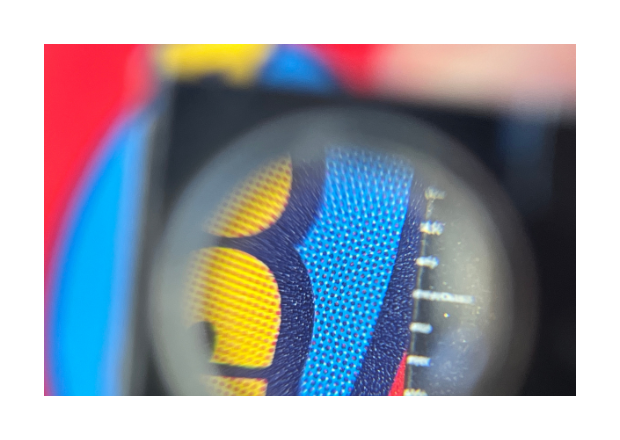
Printed Metal Packaging
When durability matters choose metal packaging. When durability and quality branding matters choose printed metal packaging. Offset printing is an industrial process that delivers excellent results and offers a host of benefits to your business.
The Offset Printing Process
Industrial metal packaging is printed using the offset printing process. This technique is ideal for producing large volumes of printed packaging when quality and efficiency matter.
The name "offset" comes from the fact that the ink is offset from the plate to the rubber blanket and then to the metal. It is also called modern lithography and it is the process used to produce our printed tins.
Offset printing uses a series of rollers and cylinders to transfer an image to the flat metal packaging in four stages;

1. Prepare the printing plate
The printing plate is moistened with rollers to create a water-based film on the non-image areas.

2. Apply ink
Ink rollers transfer ink to the image areas of the printing plate. The ink sticks to the image because the printing blank is treated to repel water from the non-image areas.

3. Transfer the image
The inked image is transferred from the printing plate to a rubber blanket.

4. Press the packaging plate
The flat tinplate blank is pressed into contact with the blanket by the impression cylinder. Transferring the image from the blanket to the metal sheet.
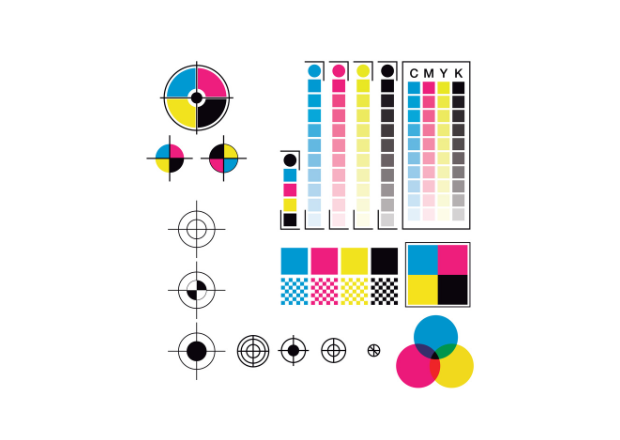
The CMYK Colour Model
The standard colour model for commercial printing is CMYK, which stands for cyan, magenta, yellow, and black. In offset printing, the colours are layered in this order and each colour is applied using a separate roller.
- Cyan: A bluish-green colour
- Magenta: A purplish-red colour
- Yellow: A bright yellow colour
- Black: Also known as "key", this colour is used to create depth and contrast
CMYK is a subtractive colour model, which means that colours are created by reducing the brightness of white with layers of ink. The amount of each colour that is layered determines the resulting colour. For example, combining cyan and yellow creates green.
CMYK is different from the RGB model used in digital displays. In CMYK, physical ink colours are used, while in RGB, the colours are combined digitally. This is why businesses need brand-specific colour codes for CMYK and RGB.
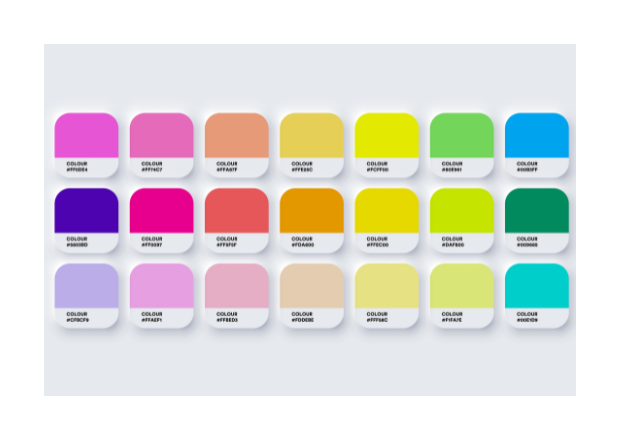
Pantone Colours
Pantone colours are a standardised colour-matching system. They are used for specific branding colours that can not be mixed using the CMYK system. If a metal packaging design needs a Pantone colour this will require an additional step in the printing process, an extra roller and specially mixed ink. This is why there is an additional cost when using Pantone colours.
Most commercial metal packaging uses a CMYK and Pantone print, CMYK for the bulk of the design and Pantone for the brand colour.
The business benefits of branded containers
Offset printing is a good choice for high-volume printing because it produces fewer emissions and wastage, and has a lower per-unit cost. It also works well on metal and produces durable, high-quality images.
Printed packaging is more professional and durable than paper labels. Paper labels can be damaged during shipping and handling meaning important product guidelines and safety information can be misread. Offset printing is the best labelling choice when packaging products that need to display hazard goods labels such as solvents and chemicals.
The visual quality of industrial printing elevates your packaging and your product. It ensures your brand colours stand out and gives customers confidence in your product before they even open the tin.
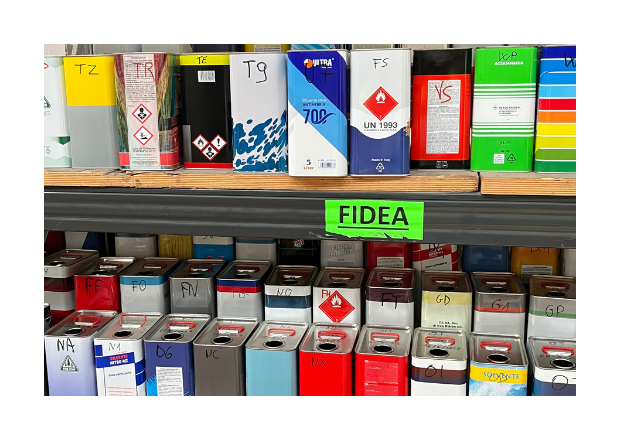
Industry uses
Printed metal packaging has been around for a long time and it has remained popular for a reason. It is practical, durable, and trusted by consumers and manufacturers alike.
Metal recycles forever making it one of the most sustainable packaging choices, and the market trend for metal packaging is on the up as businesses switch away from plastic and back to metal.
Metal packaging is used in a wide variety of industries including;
- Paints and Coatings - The 2.5L and 5L paint tin is a practical classic.
- Food Oils - Olive oils and other edible oils are often packaged in brightly-coloured rectangular tins.
- Engine Oils and Automotive Additives - Berg-top metal cans are a practical choice when products need to be decanted and re-sealed, making them ideal for automotive use.
- Chemicals - UN certified packaging is a legal requirement when packaging dangerous substances, making metal rectangular tins a popular choice for solvent and chemical producers.
Printed Packaging FAQs
What type of metal packaging is suitable for offset printing?
Both our round and rectangular tins are suitable for offset printing. In both cases, the flat plate is printed before the cans are formed, so the decision needs to be made before you place your order.
What’s the lead time for printed packaging?
It depends. It typically takes a few weeks for plate to be printed. However if plate is printed and kept in stock ahead of when it is needed, turnaround is much quicker.
How much does it cost to have tins printed?
The cost depends on the number of colours used and the quantity ordered. Speak to your account manager or get in touch for a quote.
What are the MOQs for printed tins?
Offset printing is an industrial process so it is only suitable for larger orders. Speak to your account manager or get in touch to find out what the MOQs are for your product
Do you offer a design service for printed tins?
Yes. Whether you need a design update or full design support our in-house team, Invo Design can help. Request a call here.
Find out more
Speak to your account manager or get in touch if you’d like to find out more about printed packaging. We have decades of packaging experience and our own in-house design team, Invo Design, so whatever you require we are here to help.